However, as the growth of the vinyl market exceeded even the most optimistic projections and previous Panasonic profit centers like plasma HDTV shrank, Technics’ Home Entertainment Business division—headed by Michiko Ogawa, an engineer who in 1988 helped develop Technics’ AFP1000 ultra-thin, large-diaphragm loudspeaker, and is also an accomplished jazz and classical pianist—re-entered the two-channel audio market and recommitted to making turntables (footnote 1).
At the 2016 Consumer Electronics Show, Technics announced a new SL-1200 aimed not at DJs but at audiophiles. The new hand-assembled SL-1200, available in various versions (footnote 2), looked like the old SL-1200, but inside it was brand new: every one of its hundred-odd parts—which Technics displayed on a wall at last September’s Tokyo International Audio Show—had required retooling (footnote 3).
More recently, Technics came up with another surprise: a new servo-controlled version of the legendary SP-10, the world’s first direct-drive turntable, introduced in 1970 and intended for use in broadcast studios. In 1975, Technics had introduced the SP-10Mk.2, with quartz-locked speed control and external power supply. Technics also introduced the SL-1000Mk.2—a ready-to-play system that included the SH-10B3 Obsidian base and the renowned EPA-100 tonearm and, sometime later, the EPA-500. In 1981, Technics introduced, mostly for sale in Japan, the SP-10Mk.3, which had a 22lb platter and pitch control with a digital display.
Though the more costly and sophisticated SP-10 series was originally intended for use in mastering studios and radio stations—a pair of SP-10Mk.2s drive the lathes at Bernie Grundman Mastering—many found their way into the home systems of audiophiles, housed in high-mass custom plinths.
So news of a hand-built-in-Japan SP-10, after a hiatus of almost 40 years, was big news indeed. Although the Technics SP-10R looks like previous SP-10s, it, too, is new; the motor in particular is an all-new design. Production will be limited to however many SP-10Rs Technics can build. I suspect that demand has already swamped supply.
The SP-10R is essentially a motor and a platter on a (mostly) metal chassis—what Garrard and other suppliers to the broadcast industry used to call a transcription motor unit—and Technics has made sure that it can be used as a drop-in replacement for older SP-10s in existing plinths. Alternatively, you can buy the new SL-1000R reviewed here: an SP-10R housed in a Technics-designed plinth, and with a new tonearm that’s more similar to Technics’ SL-1200–series arms than to their older (and more highly regarded) EPA-100 and EPA-500 arms (both of which make for an interesting story, but not here!). The SP-10R retails for $10,000, the SL-1000R for $17,999; both are supplied with an outboard power supply.
Turntable
Let’s start with the SP-10R turntable used in the SL-1000R, which has a coreless direct-drive motor based on the one developed for the SL-1200G. It’s a double-coil, twin-rotor design and produces enough torque to drive the ca 17.5lb platter. The upper and lower coils are offset from one another by 60° to improve the rigidity of the rotor substrate, suppress fine vibrations, and reduce self-inductance.
The motor’s outboard switching power supply, using a newly developed “unwanted noise reduction circuit,” suppresses noise that might otherwise reach the cartridge. There’s another noise reduction system to prevent noise entering through the system that communicates between the main unit and the control unit. Technics claims for the SP-10R the “world’s highest-level S/N.”
Technics claims stable rotation with 0.015% or less wow and flutter, which is considered to be the limit of what can be measured. The thrust bearings that support the platter are made of a special engineering plastic claimed to provide both high rigidity and reliability. Two stainless steel weights are placed at the bottom of the chassis to lower the center of gravity and thus help prevent vibrations. Technics claims for this system “overwhelming rotary precision and improved signal-to-noise ratio.”
An upper platter of 10mm-thick brass is laminated to a lower platter of die-cast aluminum. Embedded in this platter, near its outer rim, are heavy tungsten weights, to produce an inertial mass of approximately 1 ton.cm. A vibration-deadening layer of rubber attached to its underside completes the platter’s three-layer construction, which Technics says produces high rigidity and excellent damping of vibrations. Technics publishes a graph that suggests that both the SL-1200 series and the SL-1000R/SP-10R are better at damping vibrations than even the SP-10Mk.3. The thick, ribbed rubber mat looks like the ones used on the SL-1200 models.
Platter speed—331/3, 45, or 78rpm—is selected using controls on the SP-10R’s chassis. The outboard control unit has an OLED display that monitors accuracy of speed, and has pushbuttons for adjusting speed within a range of ±16%.
Tonearm
The tonearm that accompanies the SL-1000R will look familiar to anyone who owns an SL-1200, but, as with the various iterations of Rega Research tonearms, which look alike but sound very different, depending on price, the SL-1000R’s arm is claimed to have far lower-tolerance (tighter) bearings than Technics’ less-expensive arms, and is 10″ long (254mm, or 239mm from pivot to spindle), vs the 9″ arms on the SL-1200s. The SL-1000R’s arm has a lightweight, high-damping, S-shaped armtube made of magnesium; a static-balanced, high-precision bearing in a gimbaled system hand-assembled in Japan; and the industry-standard locking collet for the headshell. Technics doesn’t supply a headshell with the SL-1000R, instead recommending Ortofon’s LH6000 shell, but you can choose your own. In addition to the standard counterweight, Technics supplies auxiliary screw-on weights that greatly expand the range of cartridge weights the arm can accommodate: up to 31gm, including headshell.
Vertical tracking angle (VTA) and stylus rake angle (SRA) are adjustable through a range of 15mm using a rotating knurled ring that will be familiar to users of older Technics turntables. This raises and lowers the platform on which the arm is mounted.
On the plinth’s rear panel is a gold-plated, five-pin DIN jack for the phono cable.
Chassis
The SL-1000R’s massive two-layer plinth is made of bulk-molded compound (BMC) and topped with a 30mm-thick aluminum deck. The SP-10R’s chassis is a three-layer assembly of BMC, die-cast aluminum, and a 25mm-thick aluminum top panel. It all adds up to a five-layer system sitting atop four height-adjustable silicon-rubber insulating feet, each horizontally reinforced with a cylindrical, vibration-absorbing, microcell polymer tube, all contained within a die-cast zinc housing.
The armboard bolts directly to the triple-layer platter/motor section, as do the two optional armboards, one at the rear (for 9″ arms) and one on the left (for arms up to 12″ long). The mounting facilities for the two additional armboards are hidden behind thick, removable aluminum panels. The direct-bolt base connection ensures a rigid, stable physical relationship between tonearm and turntable, which is important—but in terms of ensuring the arm’s complete isolation from motor vibrations, it’s probably not so good. Still, Technics has gone to heroic efforts to damp motor vibrations at the source. When I listened to the top deck and armboard through a stethoscope with the platter spinning, I heard no noise at all.
Footnote 1: Technics, Panasonic Consumer Electronics Corporation, Two Riverfront Plaza, Newark, NJ 07102. Web: www.technics.com/us
Footnote 2: See my March 24, 2017 review of the Technics SL-1200G.
Footnote 3: You can see this array of parts in the video accompanying my conversation at the Tokyo show with Technics’ CTO and chief engineer, Tetsuya (Tony) Itani.
- Log in or register to post comments


Perhaps it’s time to consider separate vinyl and digital publications.
I know there’s a wave to be caught and ridden , but vinyl sucks and turntables are a big reason why.

Is the other reason vinyl sucks “records?”
I will guess ‘needles’ is your third big reason why vinyl sucks.
If it weren’t for turntables, records, and needles, I bet you’d like it.
I feel your pain: digital sucks, too, because ‘ones and zeroes.’ Binary code cannot recreate an analog waveform, am I right?
Ones and zeroes aren’t enough, we need all the numbers. One through nine, no maybes, no supposes, no binary. You can’t recreate sound in real space, you can’t go out into sonic space, you know, without, like, you know, uh, without analog fractions – what are you going to listen to – 011001 or 110100 trying to pretend it’s thirty-three and one third? What are you going to do when you go from here to Venus and Mars or the Dark Side of the Moon or something? That’s dialectic audio.


Hi
Bingo ! “Binary code cannot recreate an analogue waveform”.
How can we eat the cake & still have it ?
In short, Vinyl is for music performance & digital is for the sound, IMO.
Let’s hear back from partain how he thinks vinyl sucks ?
Jack L

..however analog shouldn’t be confused with vinyl; modern turntables and related hardware are marvels of audio engineering, but vinyl records suck by definition – and big time for that matter.

Hi
Yr criticism is not “ok” at all, pal!
First off, please define “analogue” your “ok” way !
Then, my question to you: have you ever own & SERIOUSLY played any vinyl to qualify to make such cross-the-board comment ?????
FYI, I own 1,000+ stereo vinyl LPs of classical music & I spend more time alone with my vinyl music down my basement audio den in the daytime more than with my darling wife. Too bad, she does not like any HiFi at all.
Good vinyl music blows any digital music out of the window, IMO.
Wait until you get the chance to auditon some, pal !!
Mind you, I play my CD/DVD & stream 4K UHD classical music perfomances with superb sounding digital sound processed by my 24bit/192KHz DAC feeding my ALL triode-tubed phono-preamp & class-A single-ended power amp. Yet, the digital sound I got so far can’t touch my vinyl music.
FYI, I just enjoyed the superb performance of French Opera Arias sung by Richard Tucker (a native of Brooklyn, NY) with the Vienna’s State Opera Orchestra conducted by Pierre Dervaux recorded/cut by Columbia Masterwork (MS 6831).
Virtually I found myself sitting at 3rd row centre in the opera house – so live, so powerful & captivating. I dropped my jaw big-time as I played this LP the first time I picked up from a thrift store nearby for a buck & half !!!
Listening is believing
Jack L

Great review, thank you. I cannot wait for the OMA plinth/SAT impressions.
fwiw, the thread hijack above for analog vs digital in 2021?!? What a pack of asshats. Partain, i’m talking to you – perhaps you could follow up with more info, lol? Or please please list your system so we can ALL lofl at your “references” by which you judge components you neither understand or could afford. All the Best

Indulging once again in “old stories”:
As a teenager, I had a Technics belt-drive SL23, along with its alignment jig that accepted a universal headshell.
It may have been summer 1978 when Peter Aczel of The Audio Critic (back when he trusted his ears to go with measurements) published an article reviving knowlege about the “Baerwald Alignment”
(aka Lofgren A, B, C, Z, whatever)
This called for nulls at 66 and 121 mm (I defy ANYONE to make use of a “120.9 mm” outer null).
Not too long after that, CartAlign came out with their etched mirrored “universal” “alignment device – same nulls – and only 30 bucks (compare to the Denessen, $100, and which “scared” me when I watch other use it from time to time.
(FWIW, the CartAlign sorta resembled a boomerang)
As MF alludes, the SL-23 Technics jig did not “match up” with 66/121 paradigm.
Once or twice, when it seemed everyone in college had a low-end Japanese turntable, I would perform a “parlor trick” – which was to request an index card, ruler, and pencil which became an alignment tool (along with a small blade screwdriver that the host must have supplied).
At least once, it turned out that one could not pull the pickup out far enough to get two nulls. So I pulled it out all the way, twisted to align “at 66” and called it good.
Good Deed accomplished, I had another beer.
Around the same time, I was acquainted with a fellow who had a “Connoiseur” turntable – his setup matched up nicely with my boomerang.

“a pair of SP-10Mk.2s drive the lathes at Bernie Grundman Mastering”
Please make the correction that the two turntables being used as motors to drive Bernie Grundman’s Scully lathes are Technics SP-10Mk3 model, NOT the Mark 2 turntables.
SP-10Mk3 uses the same motor as the SP-02 lathe motor for, typically, Neumann lathes, since it has the highest torque of all Technics motors. Each Scully lathe originally was belt drive and Bernie removed all the belts, gears, and associated mechanisms and replaced them with a Technis SP-10Mk3 turntable as a drive motor. For those belt-drive dogmatists or Linnies, just to let you know that your favorite audiophile records or re-issues were mastered or remastered on a lathe driven by, yes, a direct-drive turntable!
Notice in the picture the turntable has a digital display that indicates it is indeed a Mark Three model.
- https://theaudiophileman.com/wp-content/uploads/2017/05/Bern2.jpg
Perhaps it’s time to consider separate vinyl and digital publications.
I know there’s a wave to be caught and ridden , but vinyl sucks and turntables are a big reason why.
Is the other reason vinyl sucks “records?”
I will guess ‘needles’ is your third big reason why vinyl sucks.
If it weren’t for turntables, records, and needles, I bet you’d like it.
I feel your pain: digital sucks, too, because ‘ones and zeroes.’ Binary code cannot recreate an analog waveform, am I right?
Ones and zeroes aren’t enough, we need all the numbers. One through nine, no maybes, no supposes, no binary. You can’t recreate sound in real space, you can’t go out into sonic space, you know, without, like, you know, uh, without analog fractions – what are you going to listen to – 011001 or 110100 trying to pretend it’s thirty-three and one third? What are you going to do when you go from here to Venus and Mars or the Dark Side of the Moon or something? That’s dialectic audio.
Hi
HOW ?
Jack L
Hi
Bingo ! “Binary code cannot recreate an analogue waveform”.
How can we eat the cake & still have it ?
In short, Vinyl is for music performance & digital is for the sound, IMO.
Let’s hear back from partain how he thinks vinyl sucks ?
Jack L
..however analog shouldn’t be confused with vinyl; modern turntables and related hardware are marvels of audio engineering, but vinyl records suck by definition – and big time for that matter.
Hi
Yr criticism is not “ok” at all, pal!
First off, please define “analogue” your “ok” way !
Then, my question to you: have you ever own & SERIOUSLY played any vinyl to qualify to make such cross-the-board comment ?????
FYI, I own 1,000+ stereo vinyl LPs of classical music & I spend more time alone with my vinyl music down my basement audio den in the daytime more than with my darling wife. Too bad, she does not like any HiFi at all.
Good vinyl music blows any digital music out of the window, IMO.
Wait until you get the chance to auditon some, pal !!
Mind you, I play my CD/DVD & stream 4K UHD classical music perfomances with superb sounding digital sound processed by my 24bit/192KHz DAC feeding my ALL triode-tubed phono-preamp & class-A single-ended power amp. Yet, the digital sound I got so far can’t touch my vinyl music.
FYI, I just enjoyed the superb performance of French Opera Arias sung by Richard Tucker (a native of Brooklyn, NY) with the Vienna’s State Opera Orchestra conducted by Pierre Dervaux recorded/cut by Columbia Masterwork (MS 6831).
Virtually I found myself sitting at 3rd row centre in the opera house – so live, so powerful & captivating. I dropped my jaw big-time as I played this LP the first time I picked up from a thrift store nearby for a buck & half !!!
Listening is believing
Jack L
Great review, thank you. I cannot wait for the OMA plinth/SAT impressions.
fwiw, the thread hijack above for analog vs digital in 2021?!? What a pack of asshats. Partain, i’m talking to you – perhaps you could follow up with more info, lol? Or please please list your system so we can ALL lofl at your “references” by which you judge components you neither understand or could afford. All the Best
Indulging once again in “old stories”:
As a teenager, I had a Technics belt-drive SL23, along with its alignment jig that accepted a universal headshell.
It may have been summer 1978 when Peter Aczel of The Audio Critic (back when he trusted his ears to go with measurements) published an article reviving knowlege about the “Baerwald Alignment”
(aka Lofgren A, B, C, Z, whatever)
This called for nulls at 66 and 121 mm (I defy ANYONE to make use of a “120.9 mm” outer null).
Not too long after that, CartAlign came out with their etched mirrored “universal” “alignment device – same nulls – and only 30 bucks (compare to the Denessen, $100, and which “scared” me when I watch other use it from time to time.
(FWIW, the CartAlign sorta resembled a boomerang)
As MF alludes, the SL-23 Technics jig did not “match up” with 66/121 paradigm.
Once or twice, when it seemed everyone in college had a low-end Japanese turntable, I would perform a “parlor trick” – which was to request an index card, ruler, and pencil which became an alignment tool (along with a small blade screwdriver that the host must have supplied).
At least once, it turned out that one could not pull the pickup out far enough to get two nulls. So I pulled it out all the way, twisted to align “at 66” and called it good.
Good Deed accomplished, I had another beer.
Around the same time, I was acquainted with a fellow who had a “Connoiseur” turntable – his setup matched up nicely with my boomerang.
“a pair of SP-10Mk.2s drive the lathes at Bernie Grundman Mastering”
Please make the correction that the two turntables being used as motors to drive Bernie Grundman’s Scully lathes are Technics SP-10Mk3 model, NOT the Mark 2 turntables.
SP-10Mk3 uses the same motor as the SP-02 lathe motor for, typically, Neumann lathes, since it has the highest torque of all Technics motors. Each Scully lathe originally was belt drive and Bernie removed all the belts, gears, and associated mechanisms and replaced them with a Technis SP-10Mk3 turntable as a drive motor. For those belt-drive dogmatists or Linnies, just to let you know that your favorite audiophile records or re-issues were mastered or remastered on a lathe driven by, yes, a direct-drive turntable!
Notice in the picture the turntable has a digital display that indicates it is indeed a Mark Three model.
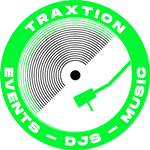